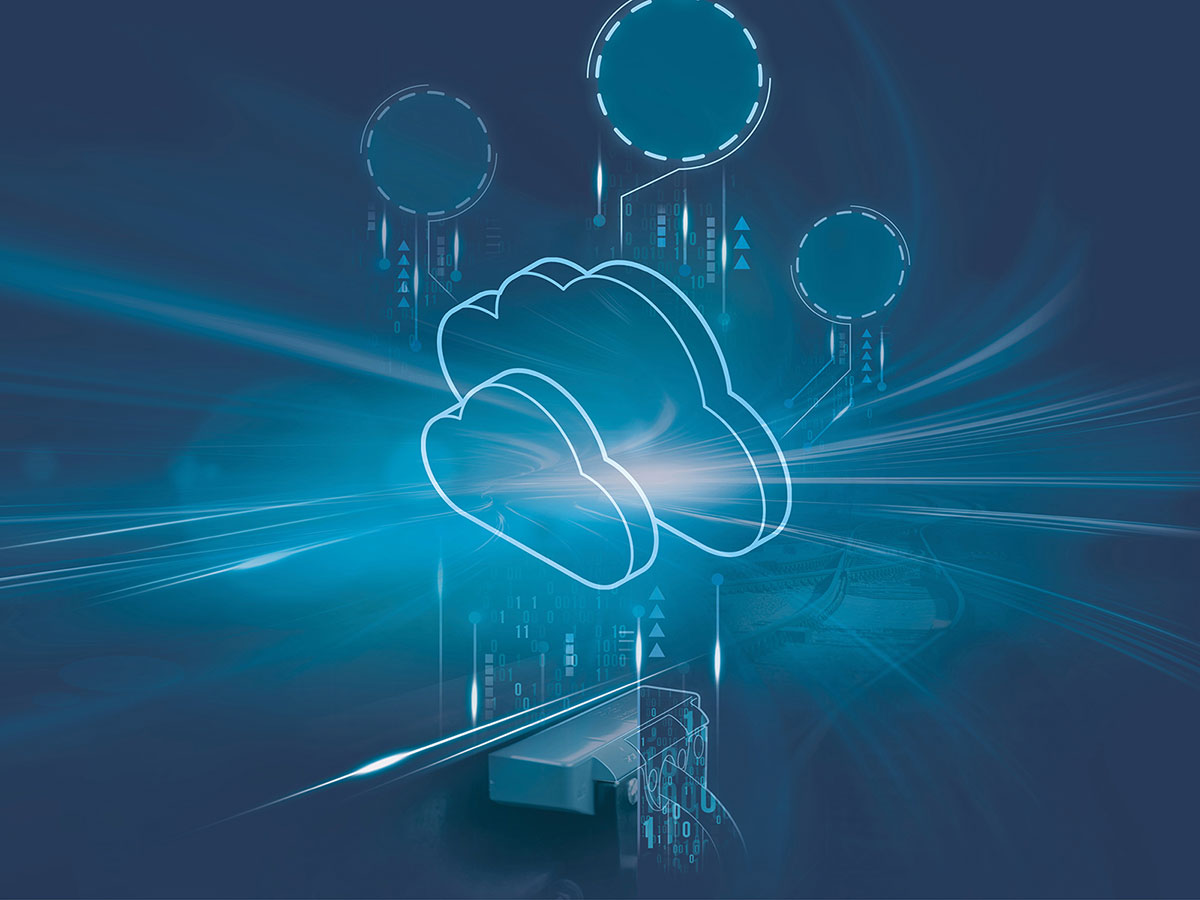
Frauscher Insights
Frauscher Insights provides easily accessible data for increased system availability and efficient railway operations. It monitors the health status of all Frauscher elements in your railway system and supports predictive maintenance capabilities with enriched data. Proactive notifications and immediate, detailed recommendations empower highly efficient troubleshooting. These capabilities are further supported by data provision in two applications: Diagnostics and Motion, ensuring the right data is always available at the right time, in the right place, and with the right level of quality.
Benefits at a glance
Optimization of railway operations
Central data storage and secure processing
Integration into higher-ranking systems is possible
Reduction of downtime through predictive maintenance
Reduction of maintenance costs
Higher reliability through efficient troubleshooting
Frauscher Insights leverages cutting-edge technologies to collect, process, and provide vast amounts of data in a secure cloud environment. This architecture enables the merging of data from different sources and facilitates advanced analytics, such as pattern comparison and anonymized data analysis across various installations. Furthermore, our connectivity manager, Frauscher Connect, ensures data security and integrity. It also acts as a unidirectional gateway, forming a barrier between the public network (IT) and the vital network (OT). This unidirectional flow ensures that while data can be collected and transmitted for analysis, there is no risk of interference or unauthorized access to the critical operational systems. This setup ensures the safety and reliability of the railway’s vital systems.
Frauscher Insights Diagnostics
Effortless access to data and alerts when it matters: Frauscher Insights Diagnostics is the higher-ranking diagnostic system that recognizes and prevents potential failures at an early stage. It utilizes data from train detection, switch point control and data transmission. This data is subsequently enriched with information and warning and error messages that are clearly displayed on the dashboard, which includes an interactive track plan. This provides a real-time display of system status, making fault detection more efficient so that downtimes can be recognized at an early stage, and possibly avoided.
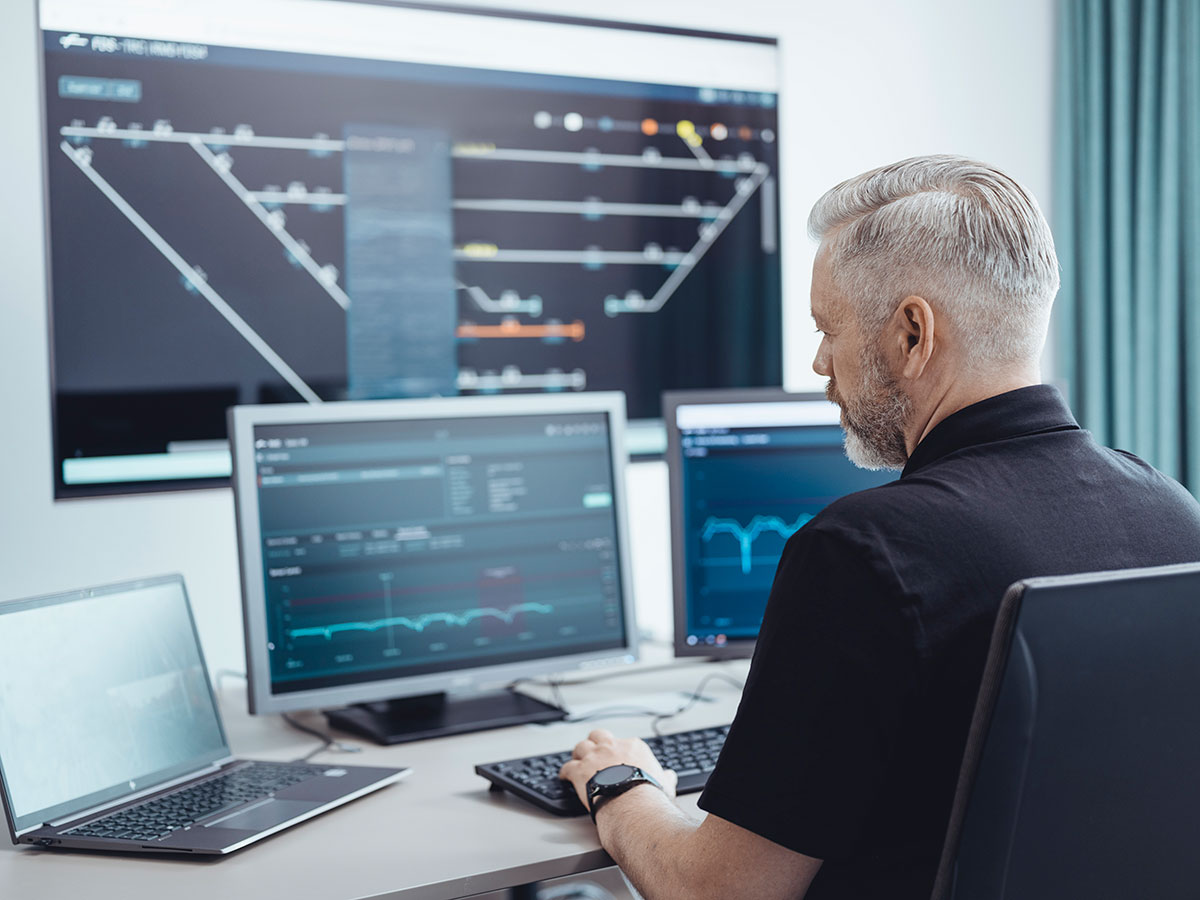
Benefits
Reduction of unplanned maintenance
Visibility of failures due to automatic notifications
Timesaving through geo positioning
More efficient use of personnel and resources
Identification of hotspots
Frauscher Insights Motion
Efficient coordination of field service assignments: Frauscher Insights Motion provides all the information needed for commissioning, maintenance and troubleshooting digitally and on the move. It makes the coordination of field service operations digital and therefore more efficient. All information is optimized for on-site use on mobile devices. This feature eliminates the need for queries and searches, while improving work efficiency for dispatchers, team leads and field technicians.
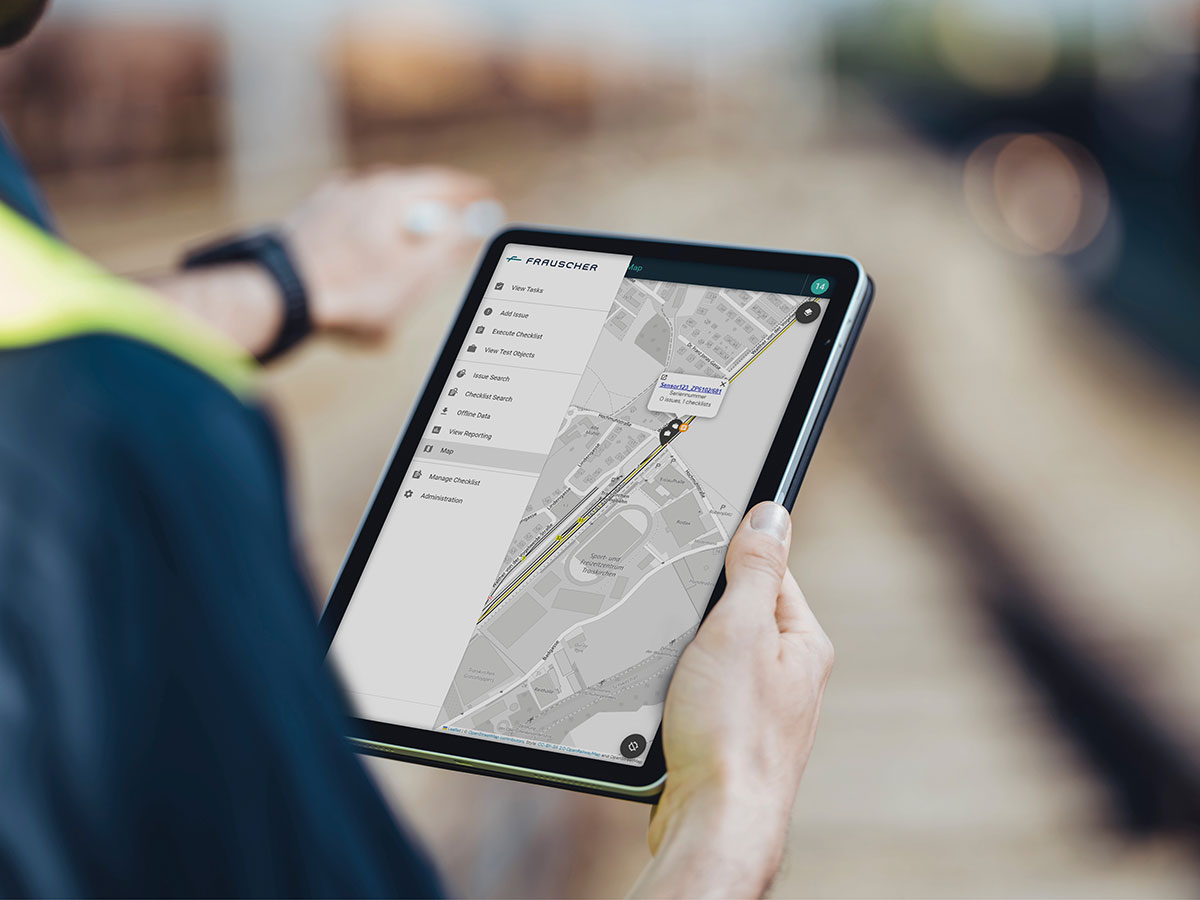
Benefits
Structured task allocation and processing
Increased efficiency of maintenance teams
Structured defect documentation
Traceability of maintenance activities
Extended report and documentation options
Flexible use through offline mode
Use cases
As safety is paramount in rail operations, component failures can trigger fail-safe states causing significant delays. Since every minute of downtime has a negative impact on traffic flow, rapid troubleshooting is essential to maintaining high performance and minimizing disruptions.
Frauscher Insights Diagnostics delivers immediate notifications to responsible personnel as soon as a failure is detected by the Frauscher axle counting system. These notifications are comprehensive, providing the identified component, error code, its meaning and actionable recommendations for resolving the issue. Additionally, precise location data is generated, ensuring that the maintenance team knows exactly where to go.
Paired with Frauscher Insights Motion, the maintenance manager can swiftly issue a work order containing all necessary details to the on-site personnel. Armed with the right spare parts and tools from the outset, the technician is fully prepared to address the issue quickly and efficiently. This smart, proactive approach not only saves valuable time but also reduces costs, ensuring that track availability is restored as swiftly as possible to keep rail traffic flowing smoothly.
This might also interest you
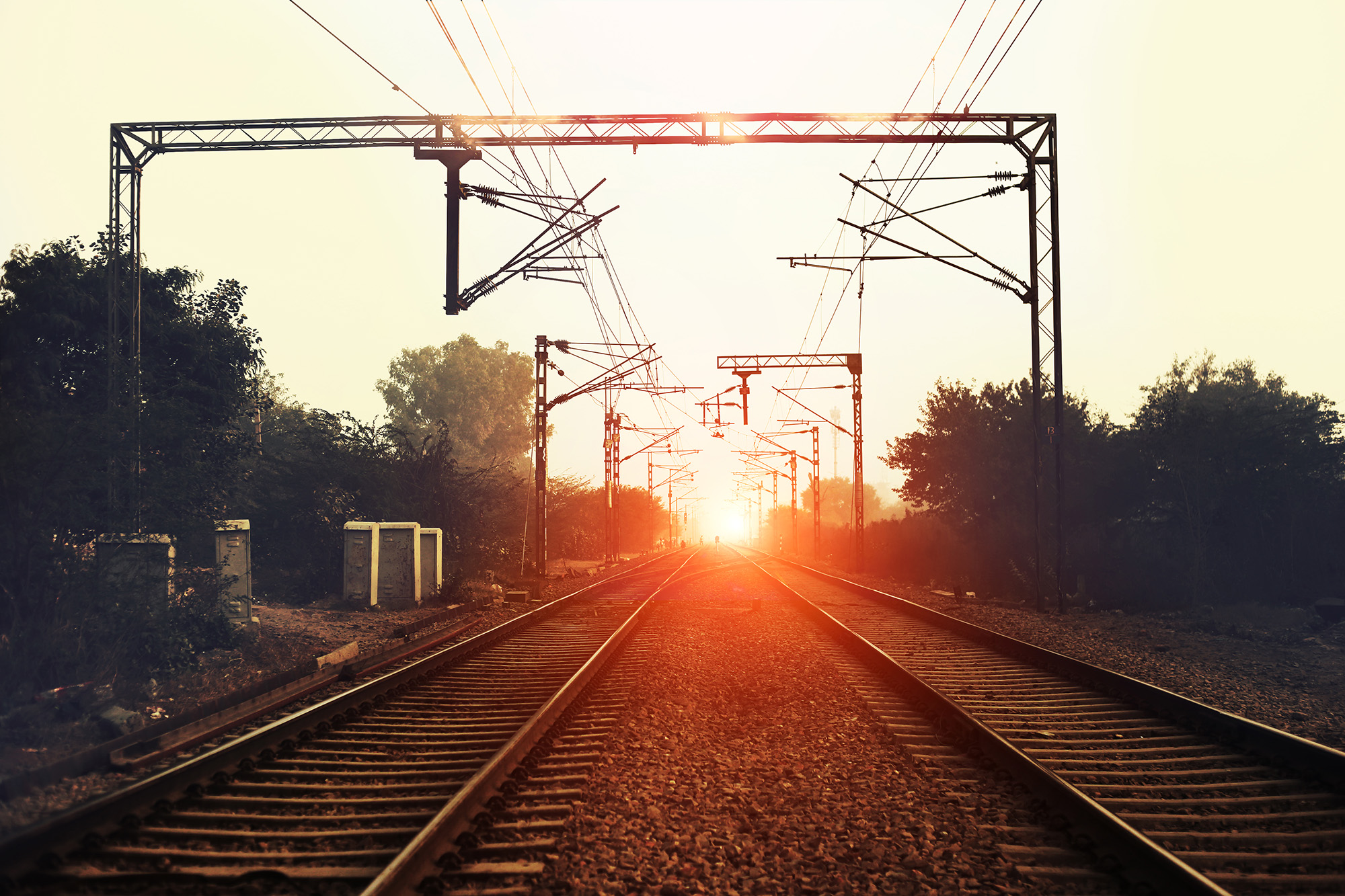
train-detection, servicesIndia
Sini - Chandil Railway Line | India
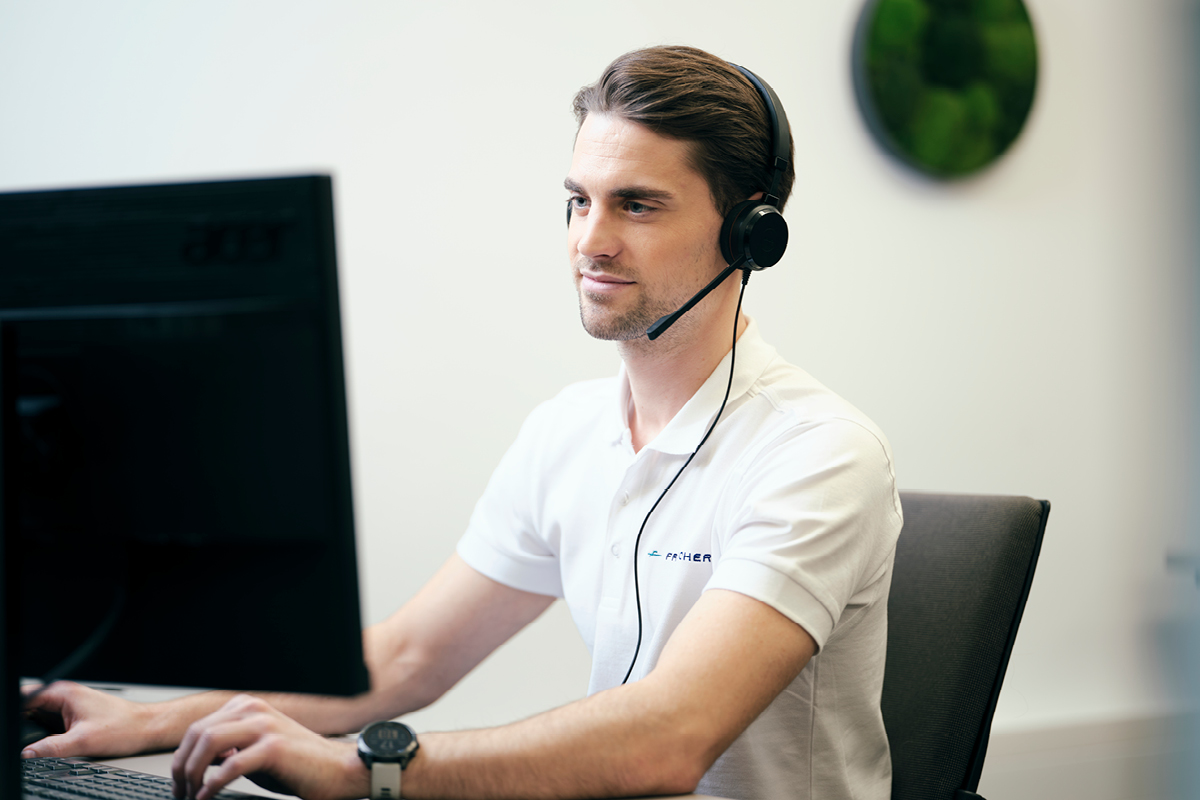
Feel free to contact us anytime!
Do you require more information? Contact us - we're here for you!