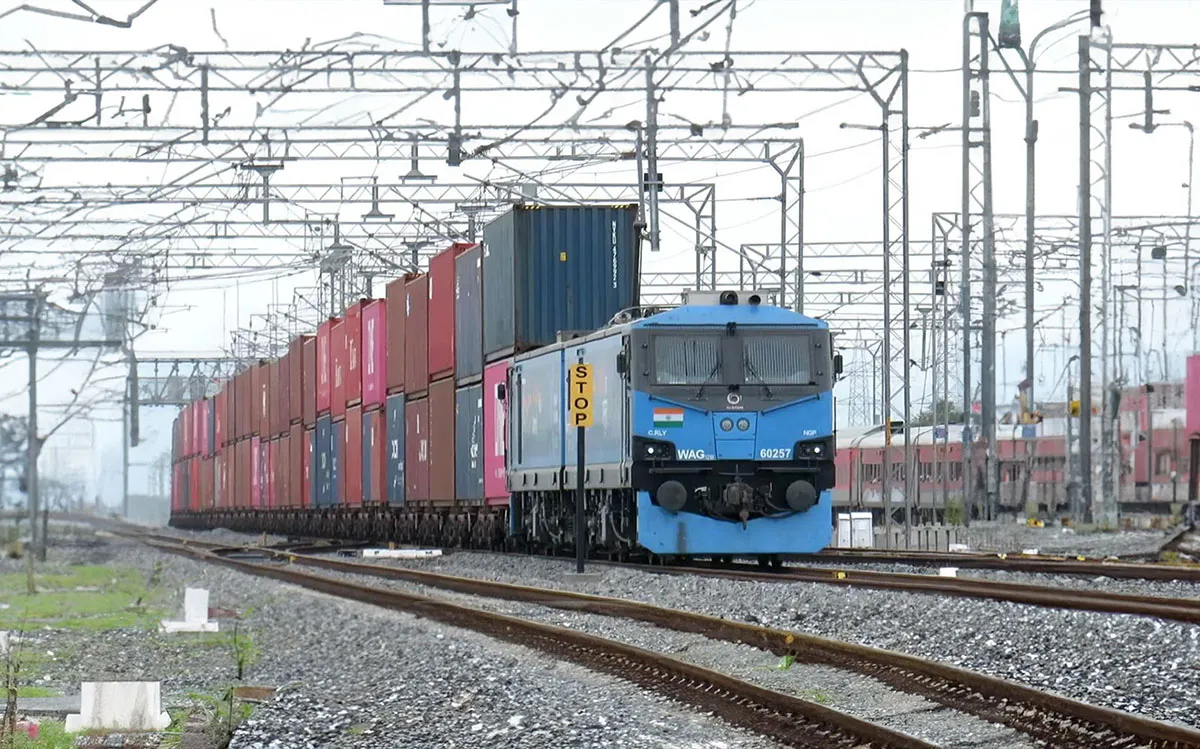
train-detectionIndia
Western Dedicated Freight Corridor (Rewari – Makarpura) | India
The Western Dedicated Freight Corridor (WDFC) represents one of the most strategically significant freight transportation projects in India. By facilitating the seamless transport of goods between major economic hubs, the intention is that the WDFC will significantly boost economic growth and development in the local region and beyond, further underlying the importance of this project.
As part of WDFC's ambitious objectives, the Dedicated Freight Corridor Corporation of India Limited (DFCCIL) sought a modern and reliable track vacancy detection system, capable of ensuring minimal downtime and optimised traffic flow, contributing to smooth and efficient rail operations.
After careful consideration, the Frauscher Advanced Counter FAdC® was selected due to the many benefits that the system presents for operators. The FAdC® fully adheres to the stringent safety requirements stipulated by Safety Integrity Level 4, making it an ideal solution for vital applications, including track vacancy detection. Furthermore, its high levels of availability and reliability contribute to an increased network uptime which in turn saves significant resources for the operator. In this case, the integration of the FAdC® into higher ranking systems including Hitachi’s electronic interlocking is done via a serial interface using the COM-FSE protocol, eliminating the usage of relays and additional wiring which reduces the overall cost, system complexity and maintenance requirements.
Seamless integration into existing systems
Frauscher Advanced Counter FAdC® was integrated quickly and easily into Hitachi’s electronic interlocking via a serial interface using the COM-FSE protocol. This has eliminated the usage of relays and additional wiring which reduces the overall cost and project complexity.
Highly resistant to adverse weather and track conditions
Wheel Sensor RSR180 functions even in adverse weather and environmental conditions with frequent flooding at the trackside.
Exhaustive technical service
Frauscher provides not only high-performance products but also detailed technology clarification and on-site training.
This project is designed according to a distributed architecture, which again significantly diminishes the necessity for extra cabling, thus lowering the overall costs. This cost saving is especially notable due to the total size of the project, featuring 4,516 counting heads. This is a unique project as a large number of counting heads are connected on one common industrial ethernet network configured for redundancy and high availability using modern networking technology. This also demonstrates Frauscher’s capability to design, configure, integrate and deliver such a large project with speed, ease and quality.
In this instance, the FAdC® was chosen in conjunction with the Frauscher Wheel Sensor RSR180 which is not only renowned for its safety in line with SIL 4 requirements, but also overall reliability, as it is used in projects worldwide with proven success. One notable benefit of the RSR180 is its resistance to adverse weather conditions such as high humidity and temperature, as well as challenging track conditions including dirt, dust and debris. The sensor also holds IP68 rating against water ingress, making it ideal for projects with frequent flooding at the trackside. The installation of the RSR180 sensors was made easy and convenient thanks to the patented Frauscher Rail Claw SK140, which eradicated the need for any drilling into the rail. Consequently, the overall cost of installation and dwell time of staff on site was significantly reduced.
This might also interest you
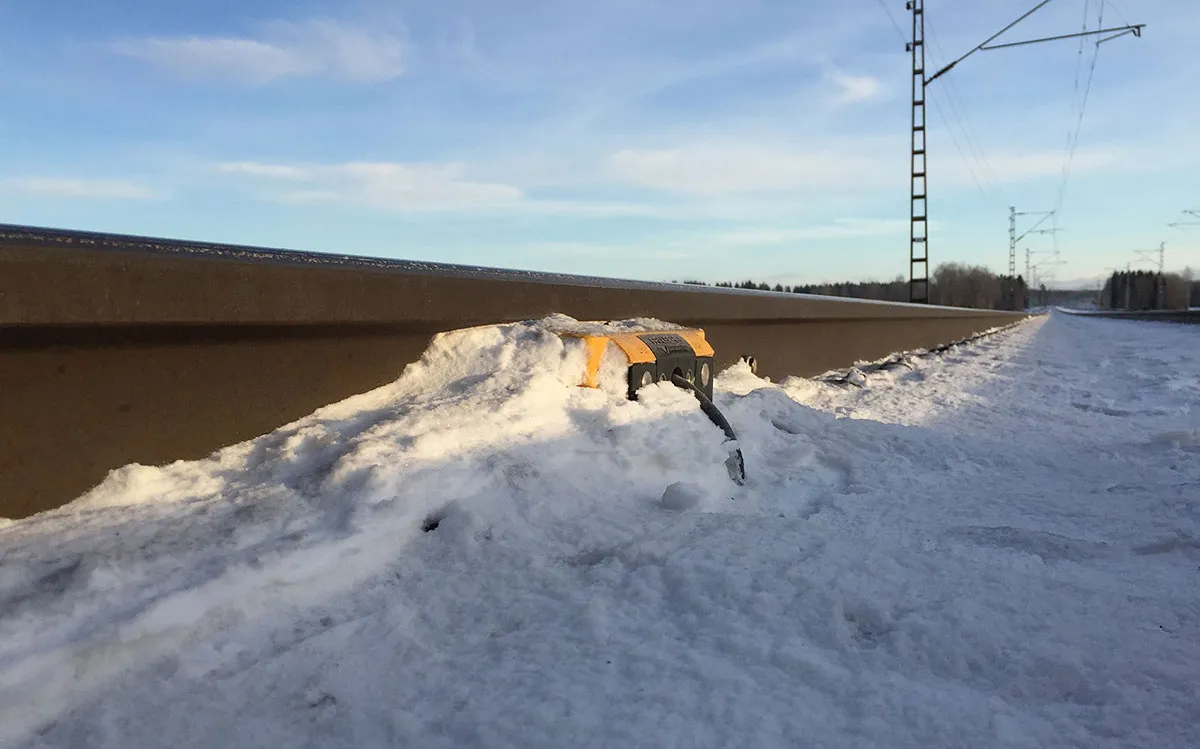
train-detectionFinland
Kokkola | Finland
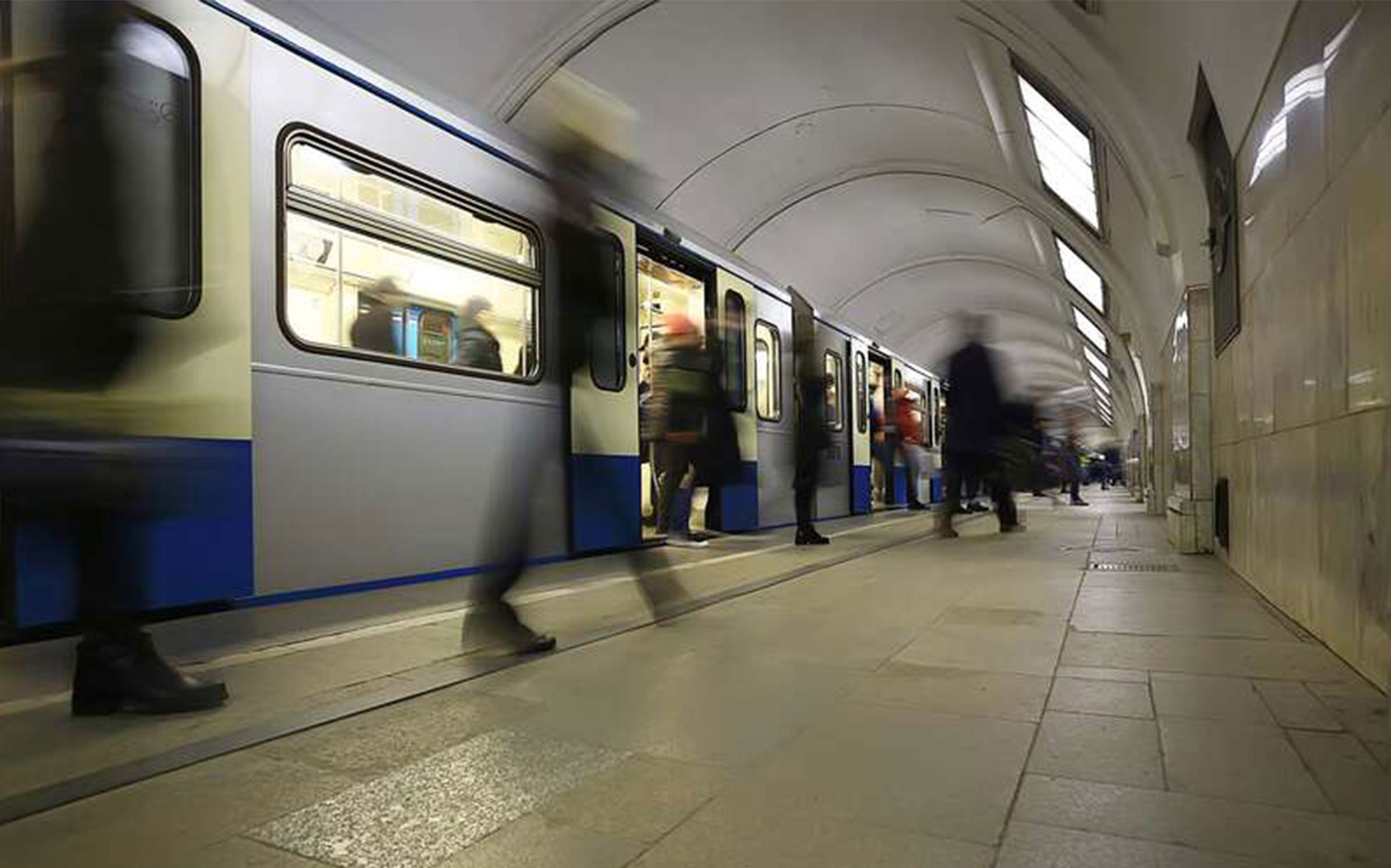
train-detectionUnited States of America
Reducing Delays in a Metro (subway) Environment | USA
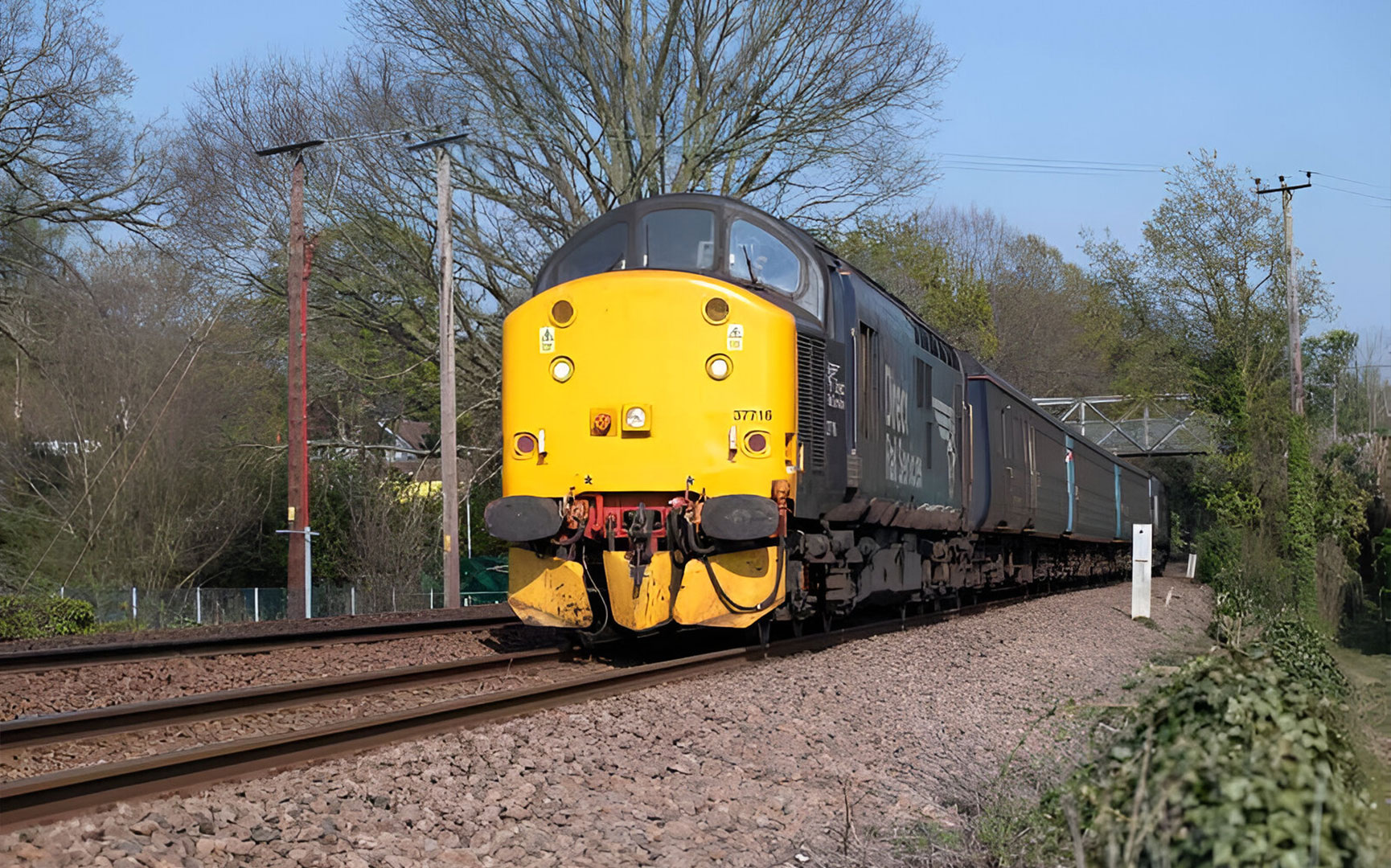
train-detectionUnited Kingdom of Great Britain and Northern Ireland
Wherry Lines | UK
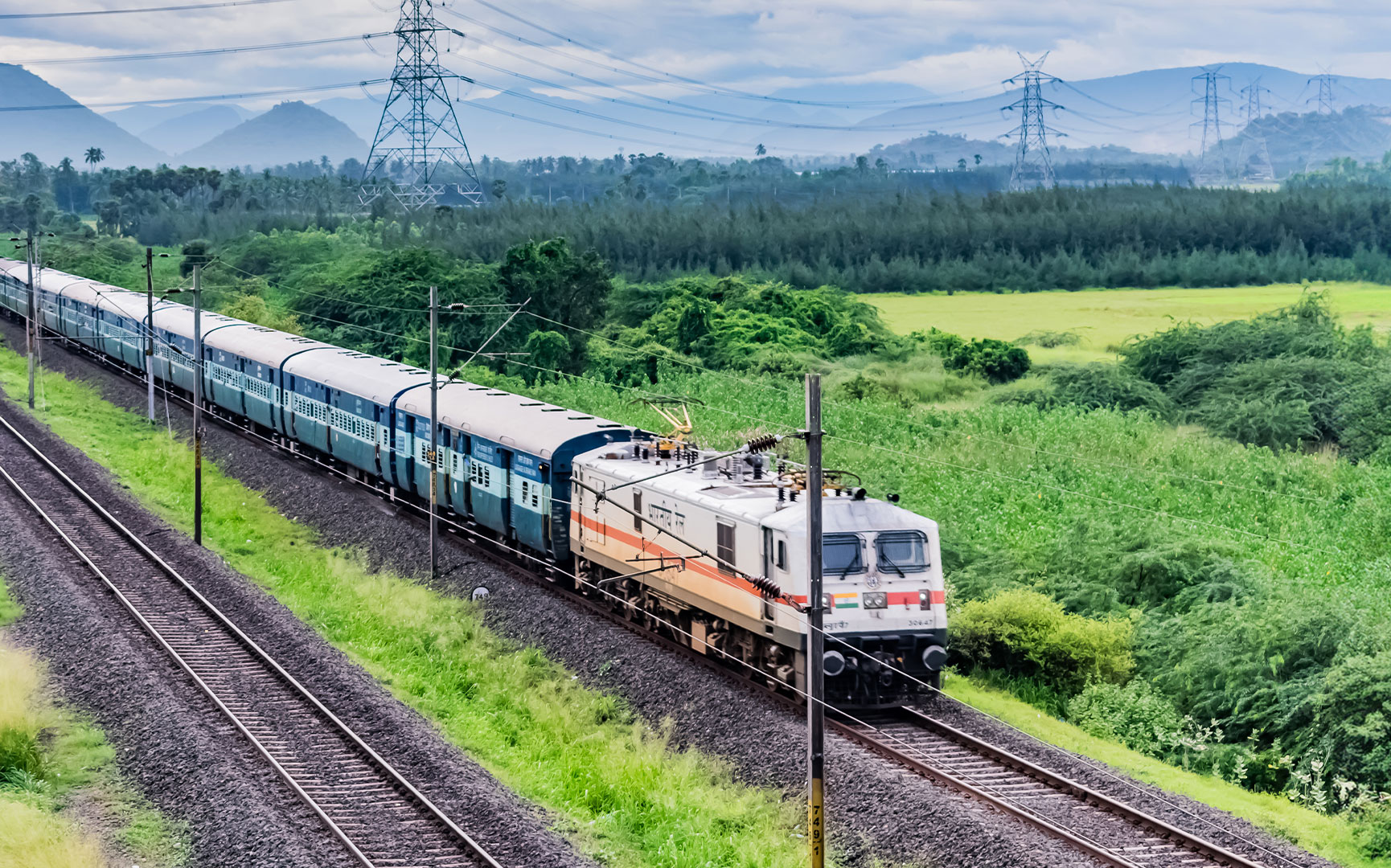
train-detectionIndia
Increasing Availability at Adra Yard | India
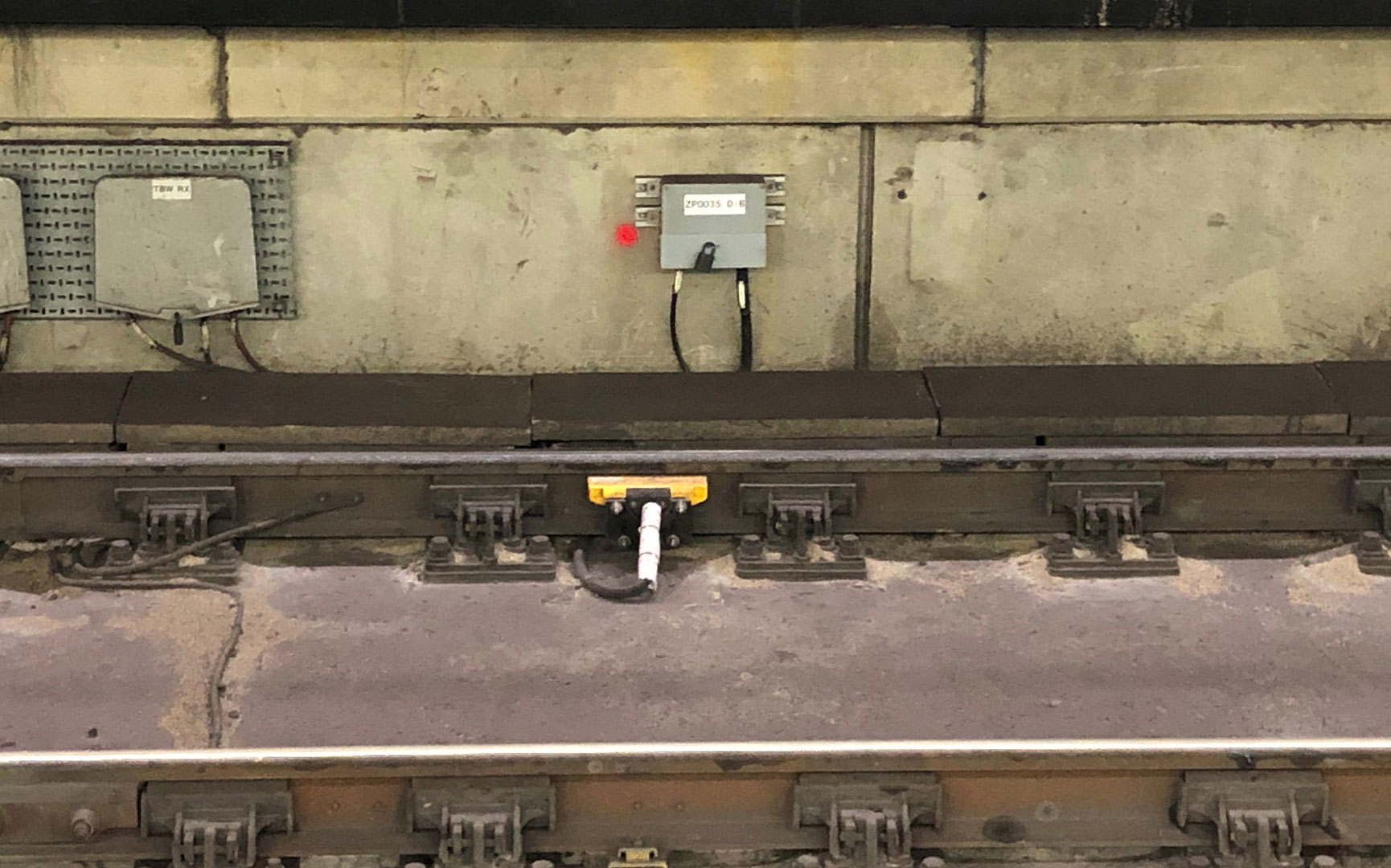