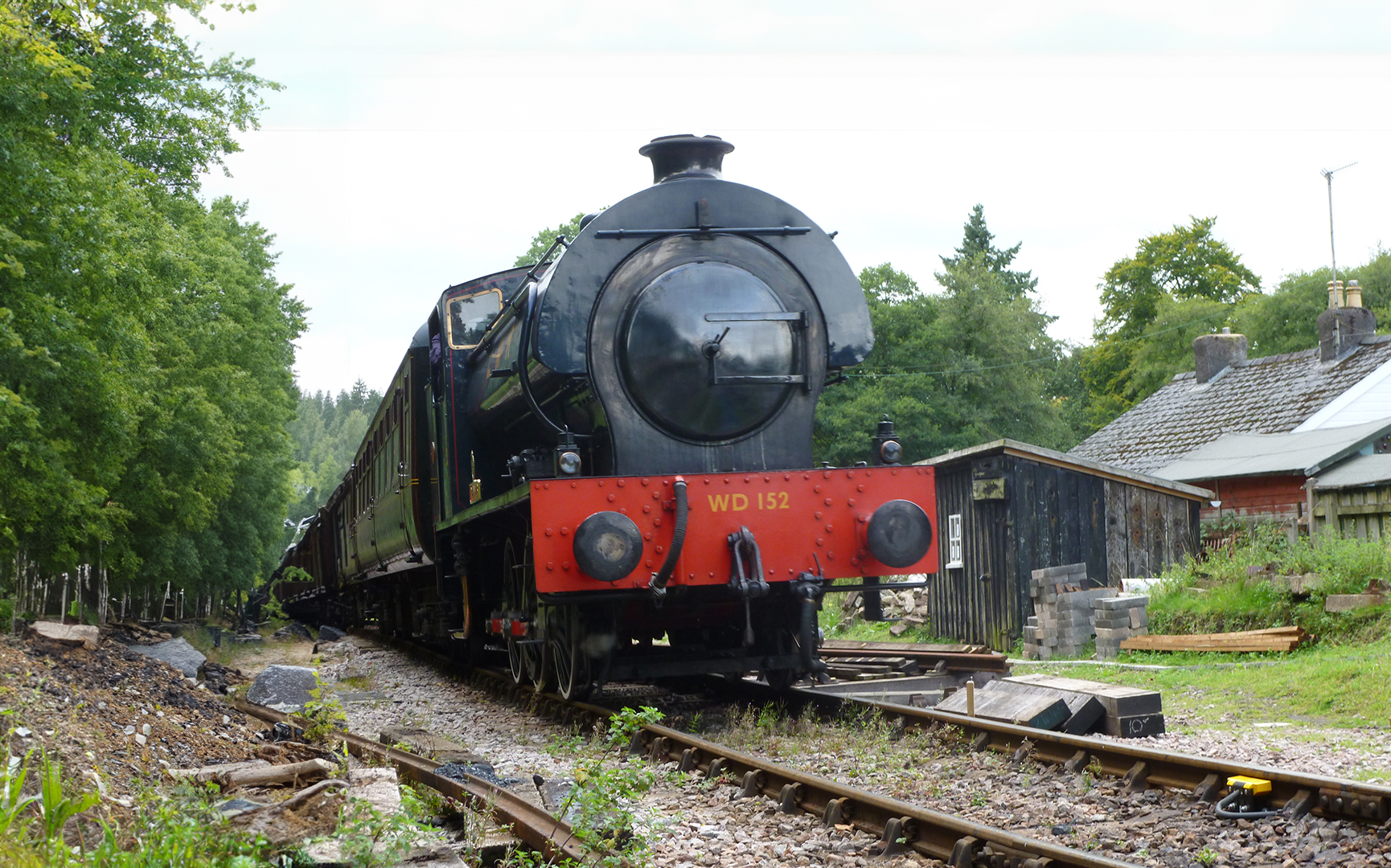
train-detection
Maintaining the past, creating the future | UK
The Dean Forest Railway (DFR) operates a historical 7 km passenger service line running north from Lydney Junction to Parkend, in the Forest of Dean. Due to extensions of the line and an additional turnout being added at Parkend, an update and modernisation of the existing train detection and signalling system was necessary. Being a heritage railway, it requires high standards in terms of signalling and safety, whilst maintaining the historical touch of the line.
The train detection system had to be integrated into the mechanical interlocking that was also being restored to bring Parkend signal box back to life. Achieving the necessary ballast resistance to reliably operate track circuits would have involved relaying a large portion of track. Together with the maintenance requirements of additional track circuits, this would have been too time-consuming, as the line is operated by a volunteer workforce. Alternatively, extending the original token system would have reduced the number of income-generating services. Thus, a different method of track vacancy detection was necessary.
Based on previous positive experiences, DFR decided to go for an axle counter solution from Frauscher. To provide maximum flexibility and meet the variety of requirements defined, the Frauscher Advanced Counter FAdC® was chosen. On track, nine Frauscher Wheel Sensors RSR123 are now detecting even the old steam train’s wheel flanges highly reliably. Using the system’s ability of establishing individual architectures, the axle counter was collocated with the interlocking inside the existing signal box. Track vacancy detection data is provided to be electronically integrated into the mechanical interlocking. Additionally, Supervisor Track Sections STS and Counting Head Control CHC are providing maximum availability and system resilience. The Frauscher Diagnostic System FDS provides DFR’s experts with remote access to real-time diagnostic data.
Quick installation
With the assistance of the Frauscher UK employees, installing and commissioning the FAdC® and Wheel Sensors RSR123 took only six days, including laying the cable. This resulted in a minimum downtime on site.
Reduction of ongoing maintenance costs
The possibility of remote diagnostics ensures that a time related benefit is given during operation as well, as it can help off duty staff members to support their colleagues onsite and reduce ongoing maintenance costs. Data configuration and consistency of spare parts, allows for future remodelling and expansion work.
This might also interest you
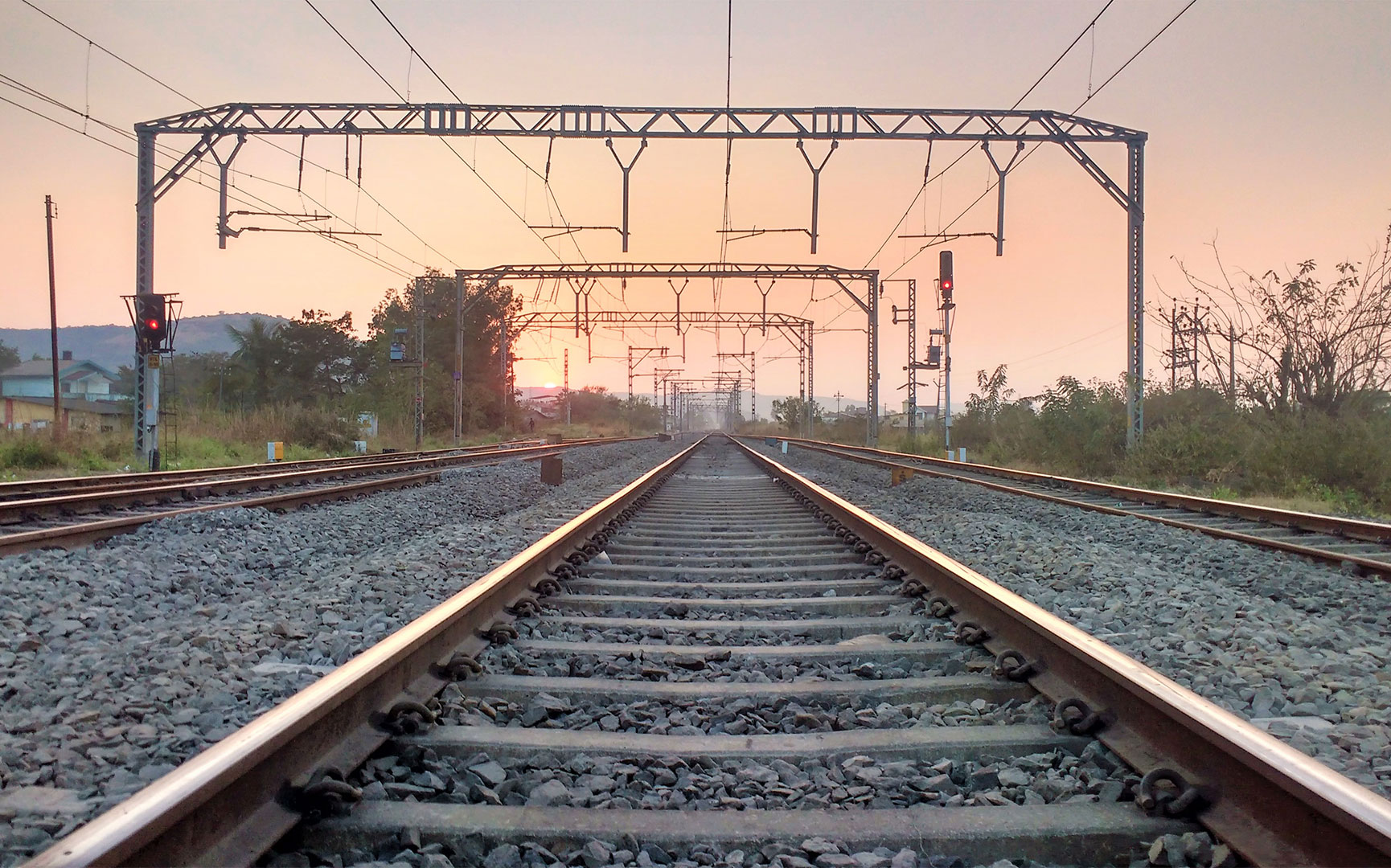
train-detectionIndia
Vijayawada – Gannavaram Rail Line | India
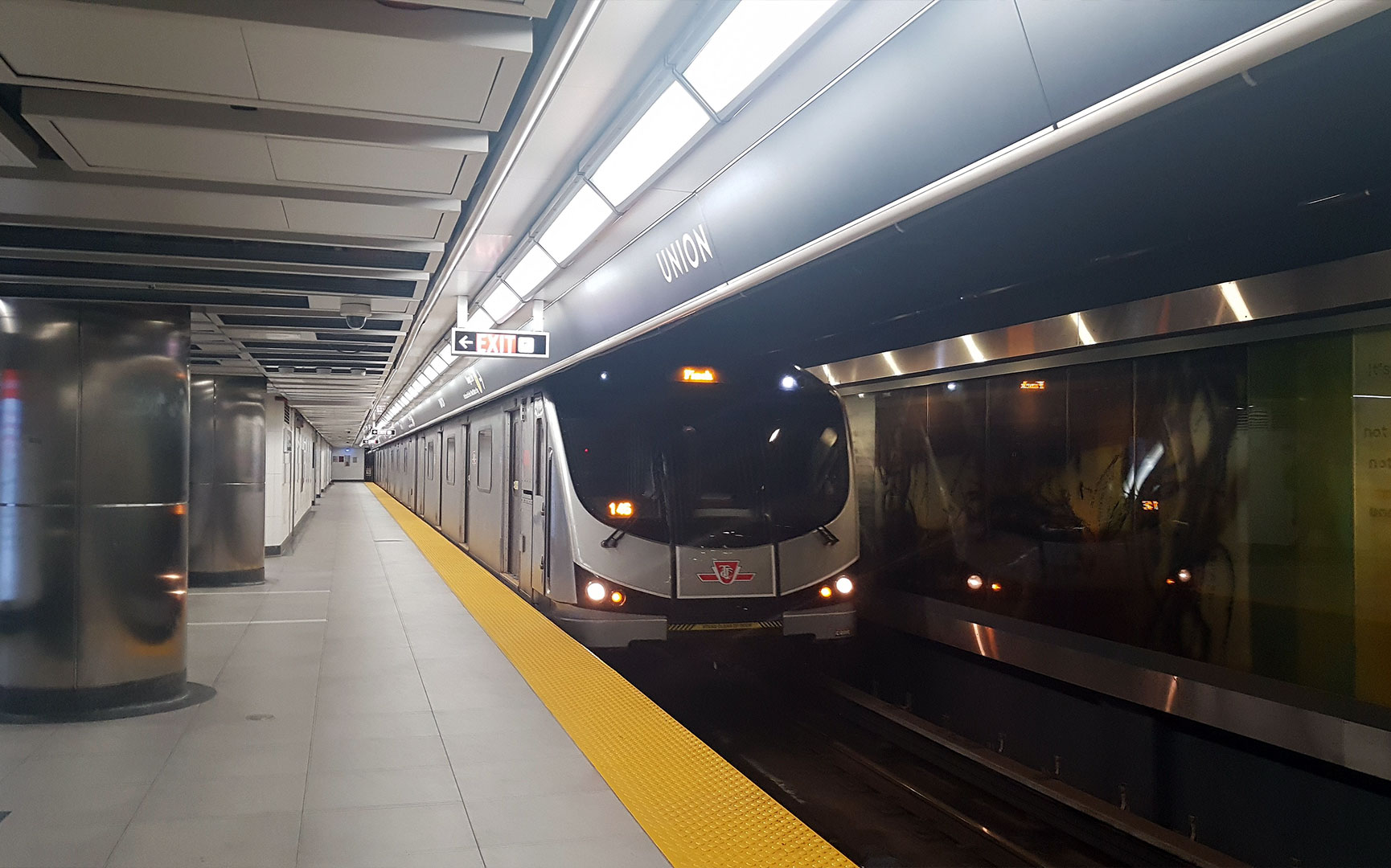
train-detectionCanada
Toronto Transit Commission | Canada
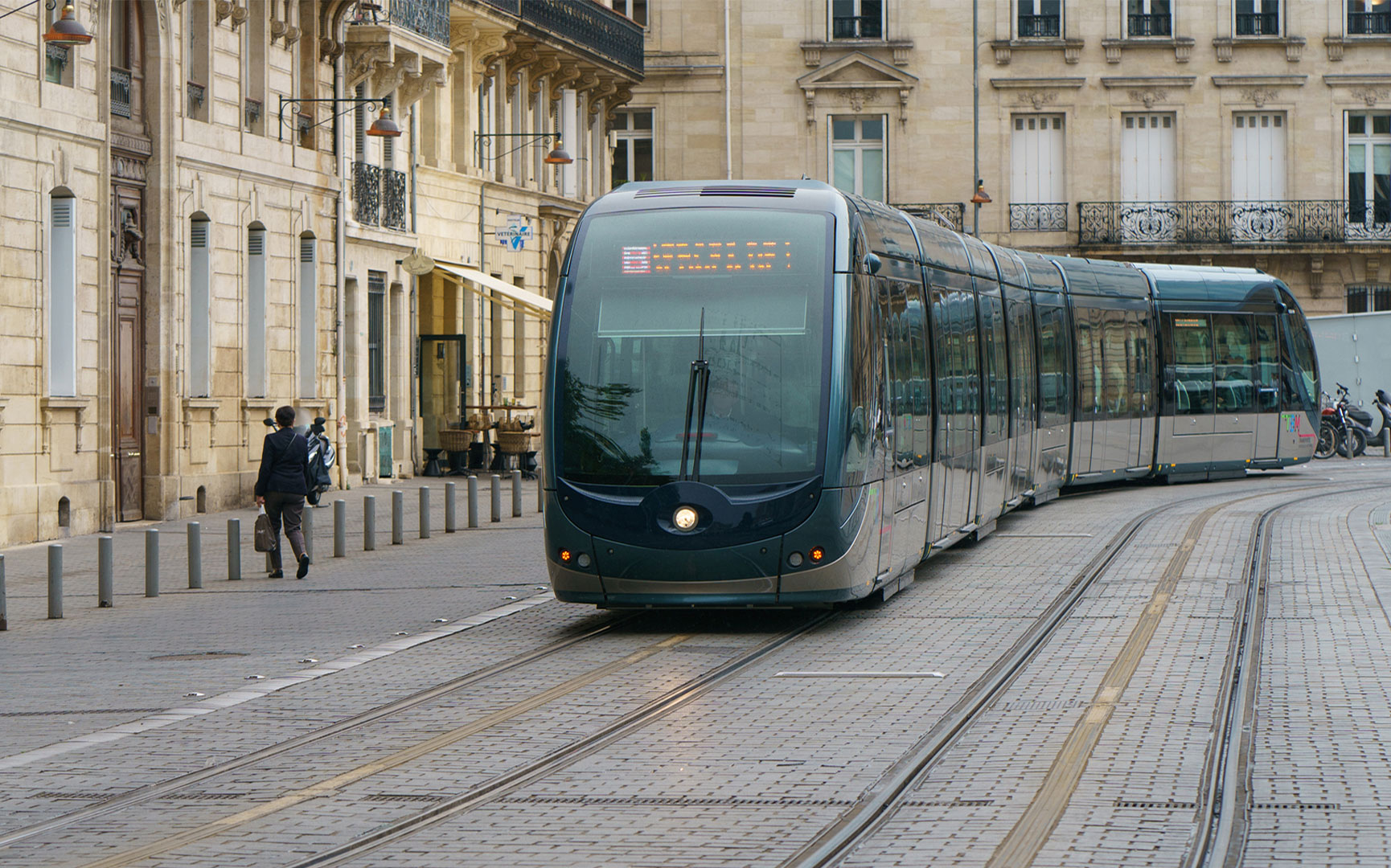
train-detectionFrance
Extension Line D Tram Bordeaux | France
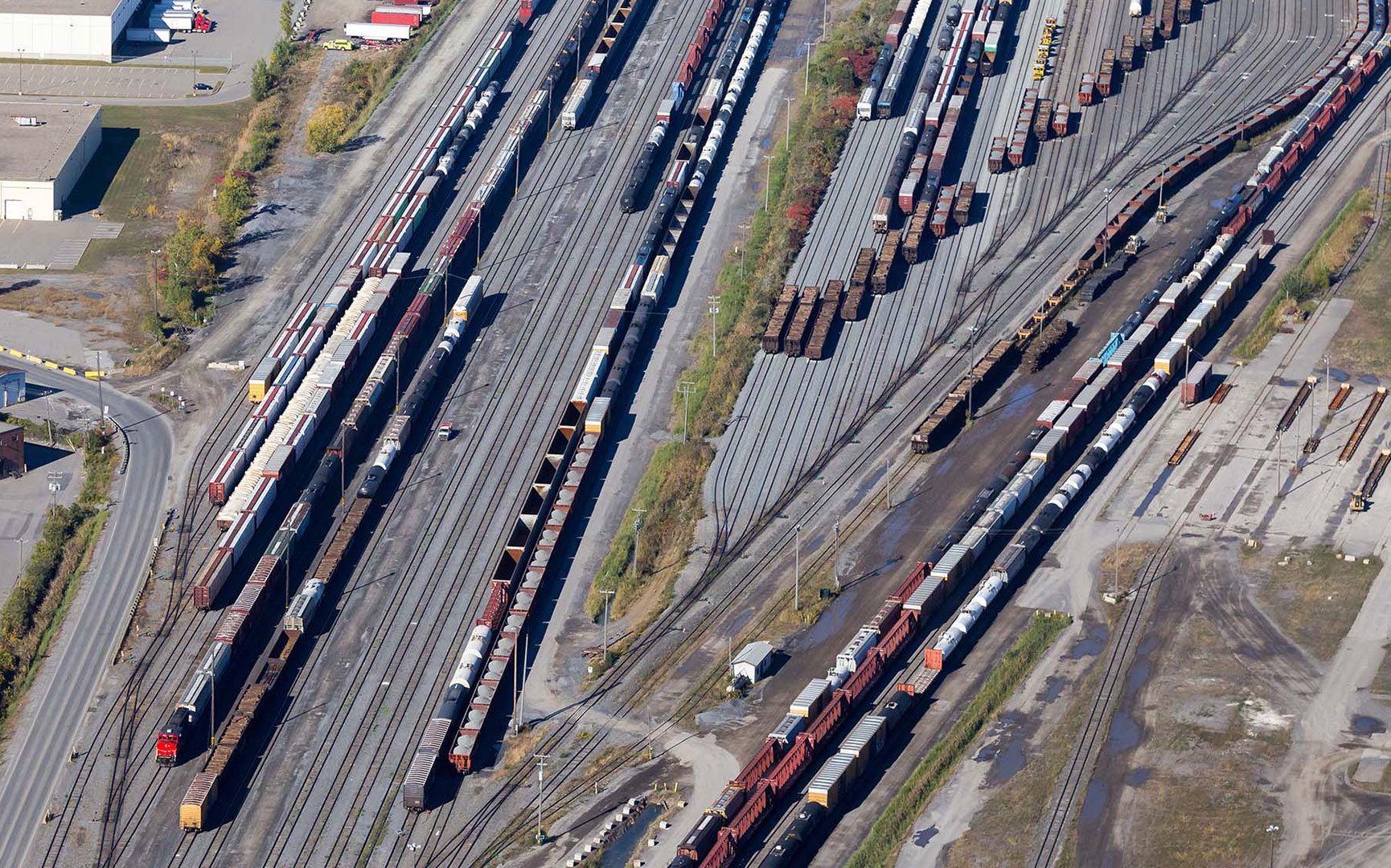
train-detectionUnited States of America
Frauscher Track Vacancy System FTVS Testing | USA
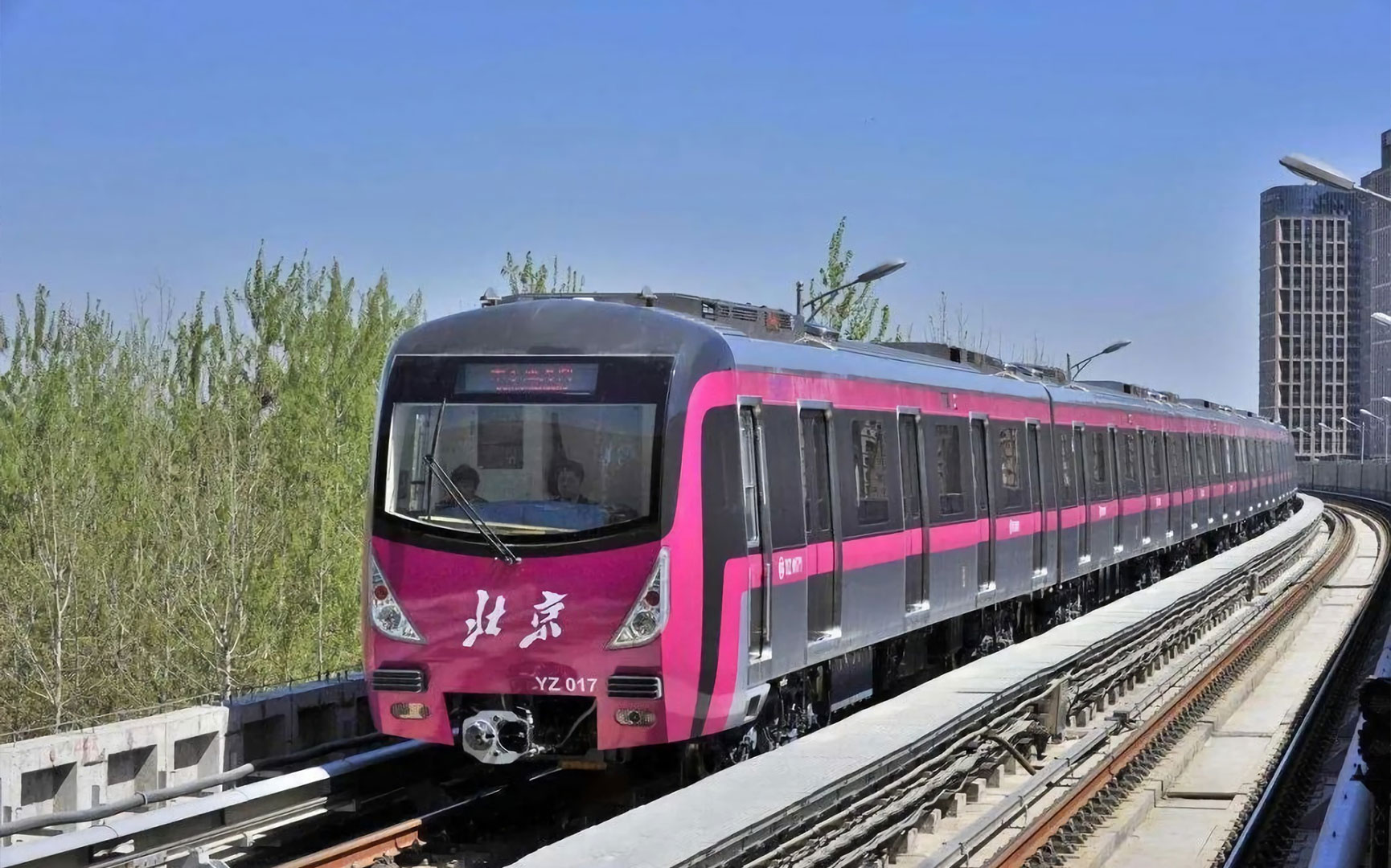