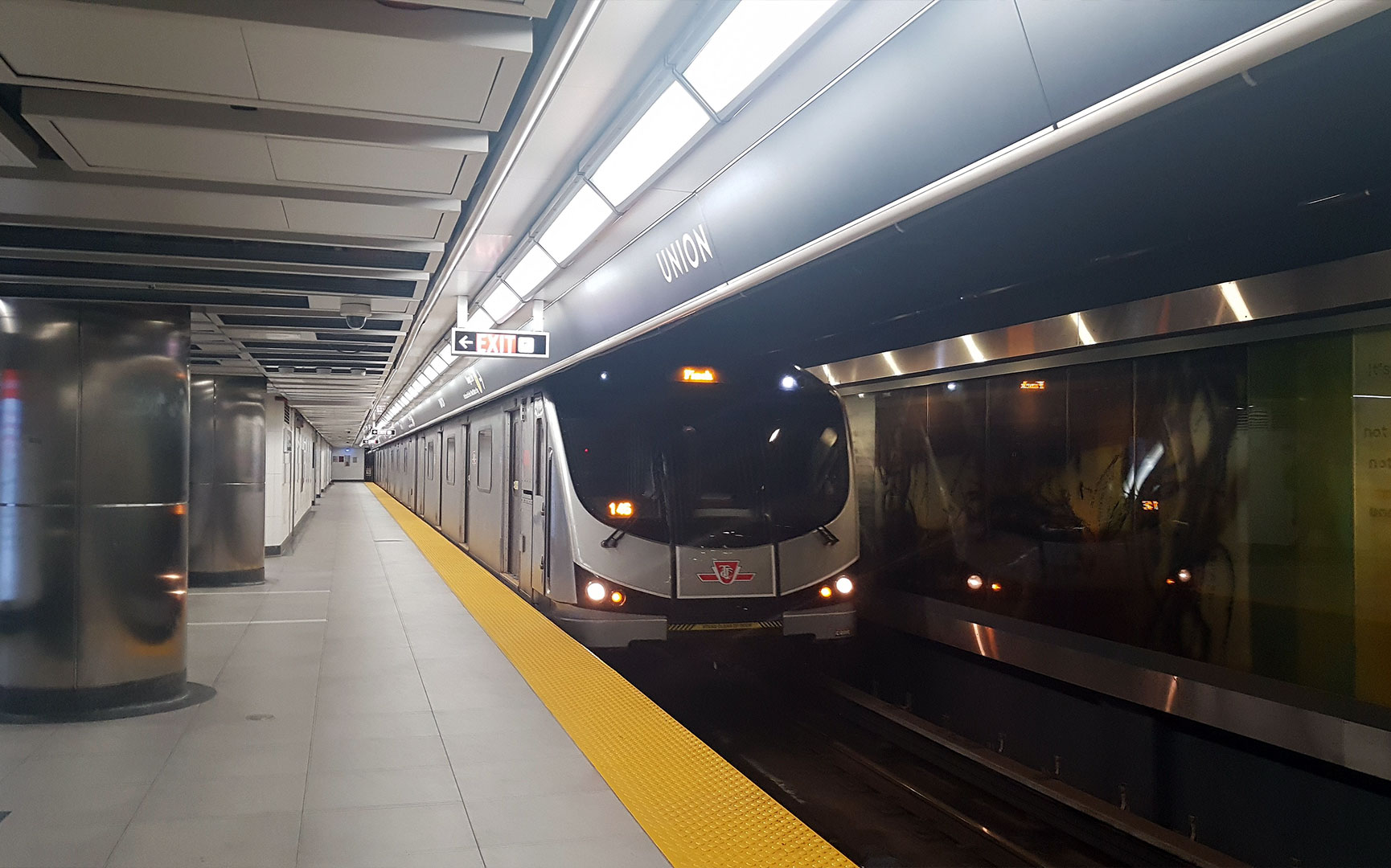
train-detectionCanada
Toronto Transit Commission | Canada
The Toronto Transit Commission (TTC) Line 1 Yonge-University is Toronto’s longest subway line, with track circuits utilized for signalling. Due to an increasing number of daily passengers and an aged system the need for upgrading without interfering with the daily operations became readily apparent. It was further required that the new signalling system functions independently of the existing system. It would provide CBTC fallback functionalities, and work as an overlay to the current track circuit-based system.
Frauscher entered into discussions with TTC to consider the benefits of Frauscher axle counters for this application. The transit needed to gain experience and further knowledge as to how the product would perform, so Frauscher offered a test trial for TTC to assess compatibility with their existing system. The trial also allowed them to test performance under conditions typical for the area, such as cold temperatures, ice, snow and road salting. Frauscher installed two Wheel Sensors RSR180 to work with the Axle Counter ACS2000. Although the scope of the test was small, TTC was able to experience how quickly and easily the system could be installed without affecting the daily operation of the busy commuter line. During the trial period of more than a year, there were zero miscounts recorded.
Due to the size of the upgrade and the need to minimize impact on daily operations, the project was broken down into several phases between 2020 and 2021. After completion, trains on Line 1 Yonge-University will be detected by 603 wheel sensors, which will form 469 track sections. The indoor equipment of the ACS2000 will evaluate the data in 31 cubicles located along the line.
Easy and quick installation
Per customer requirement, the wheel sensors and axle counters were installed without interfering with the track circuits already in place. Mounting of the wheel sensors was completed quickly, due to the use of the Frauscher Rail Claw. The rail claw is attached in about five minutes, without drilling the rail.
Increasing system availability
The ACS2000’s cost effective operation is further enhanced by use of optional add-on functionalities that increase reliability and uptime of the entire network such Counting Head Control CHC and the Frauscher Diagnostic System FDS.
This might also interest you
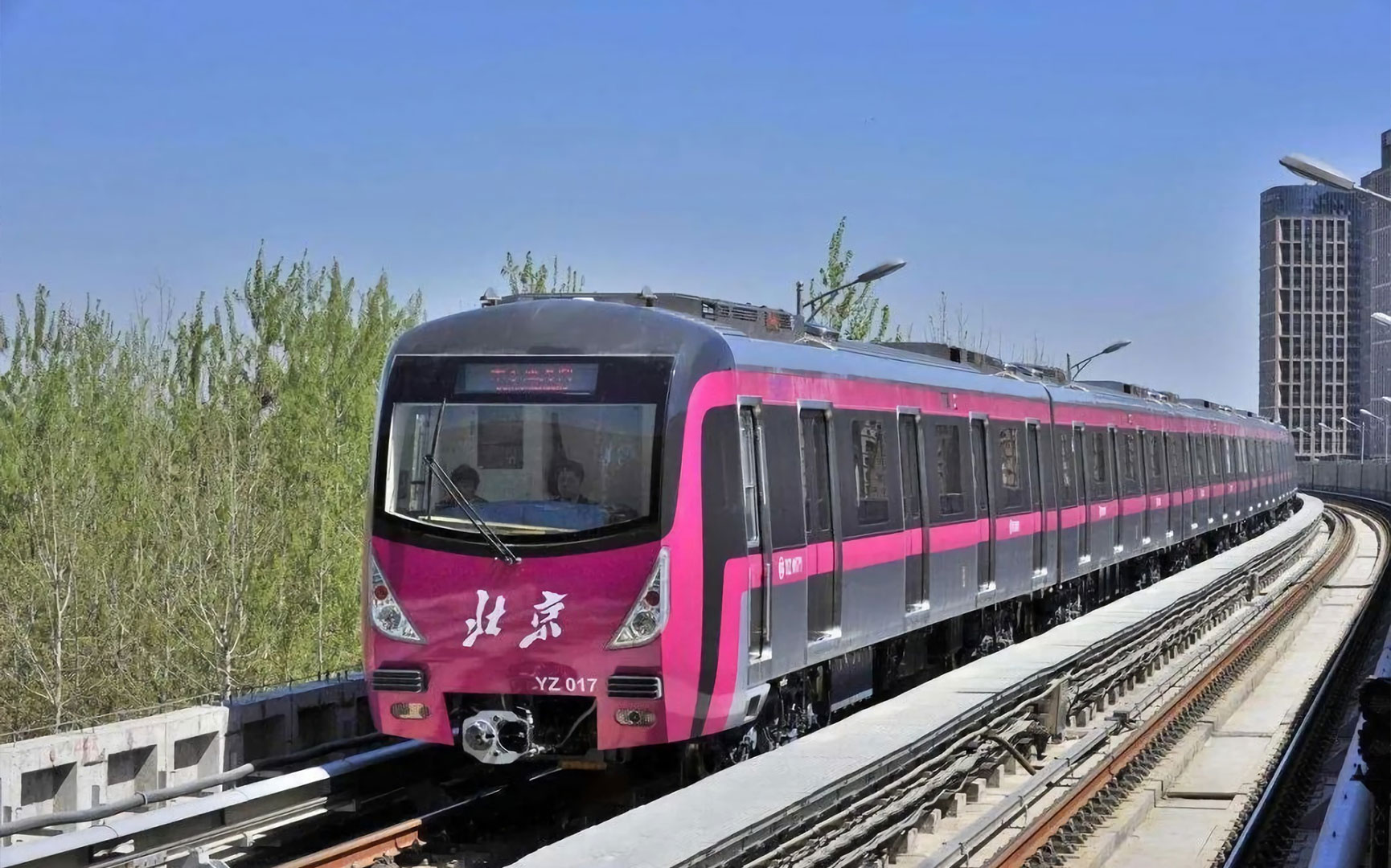
train-detectionChina
CBTC Fallback System on Beijing Metro Lines | China
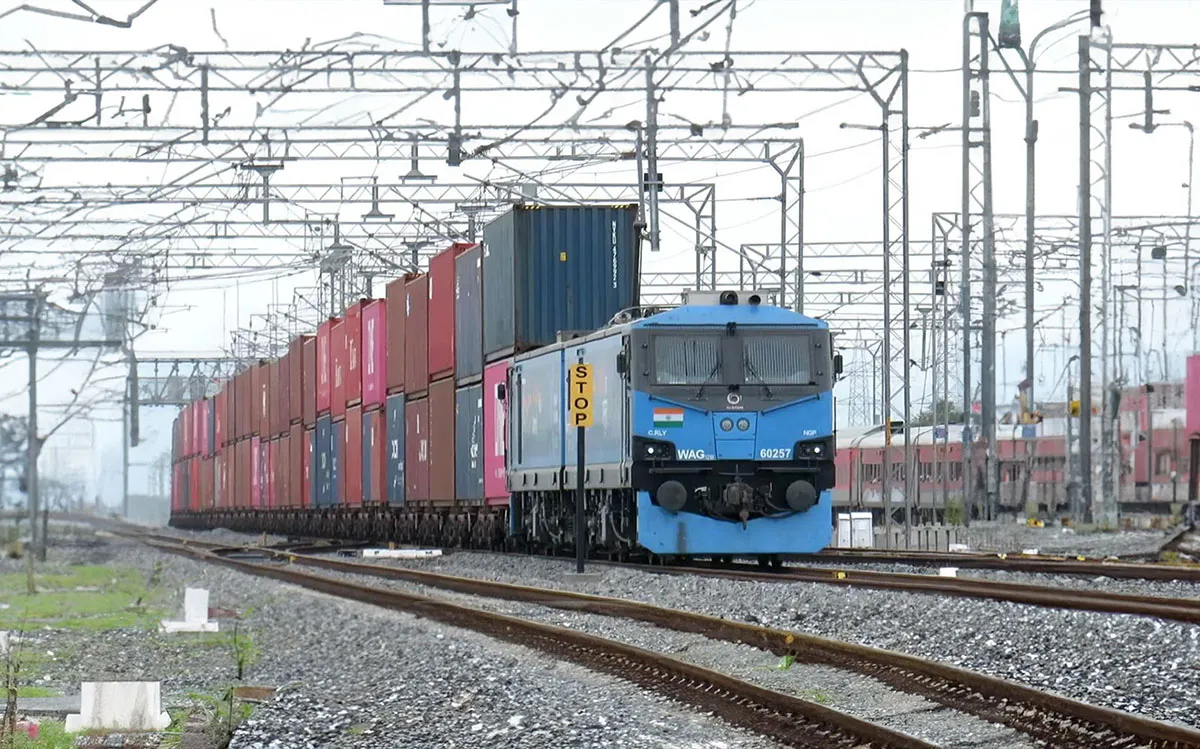
train-detectionIndia
Western Dedicated Freight Corridor (Rewari – Makarpura) | India
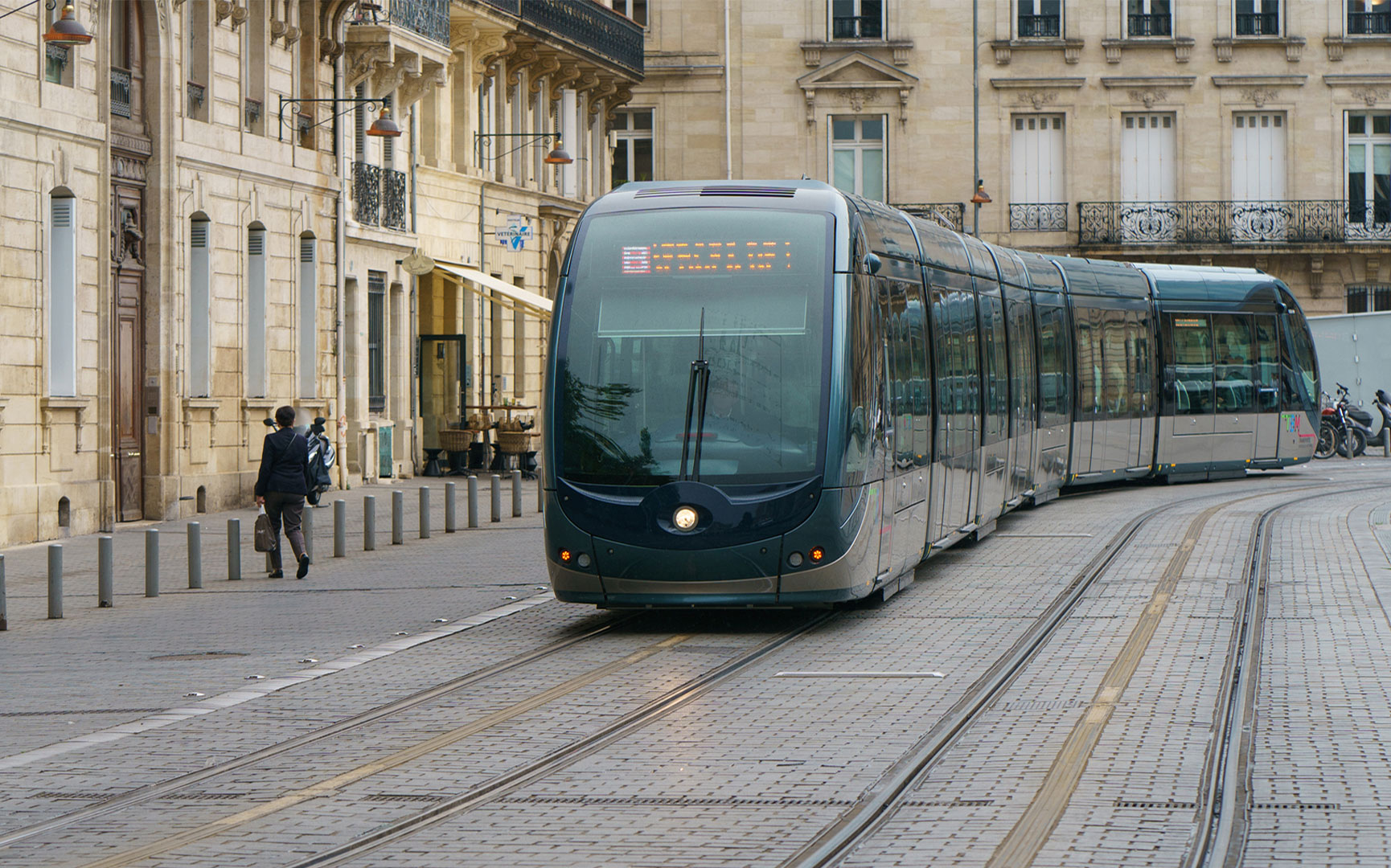
train-detectionFrance
Extension Line D Tram Bordeaux | France
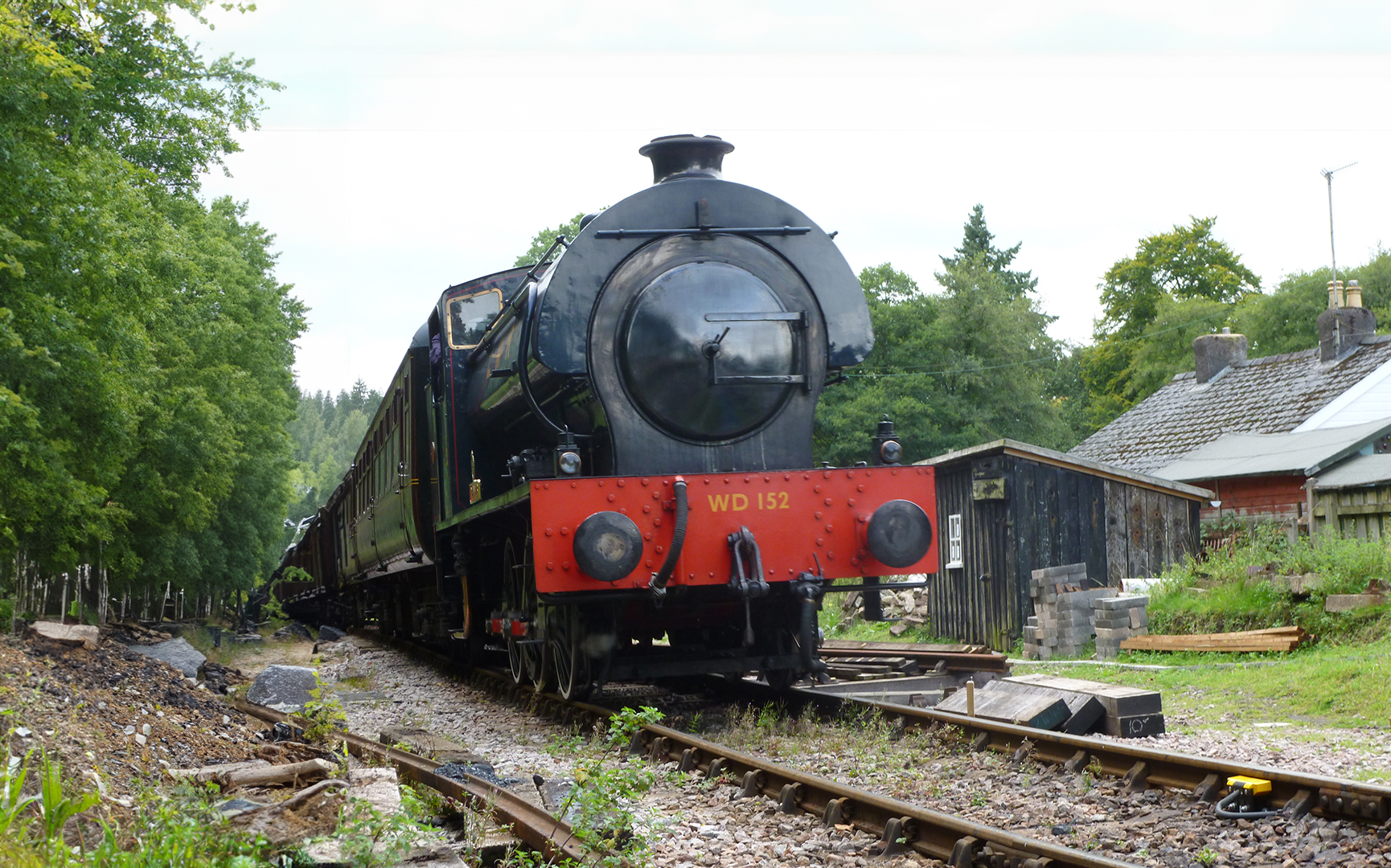
train-detectionUnited Kingdom of Great Britain and Northern Ireland
Maintaining the past, creating the future | UK
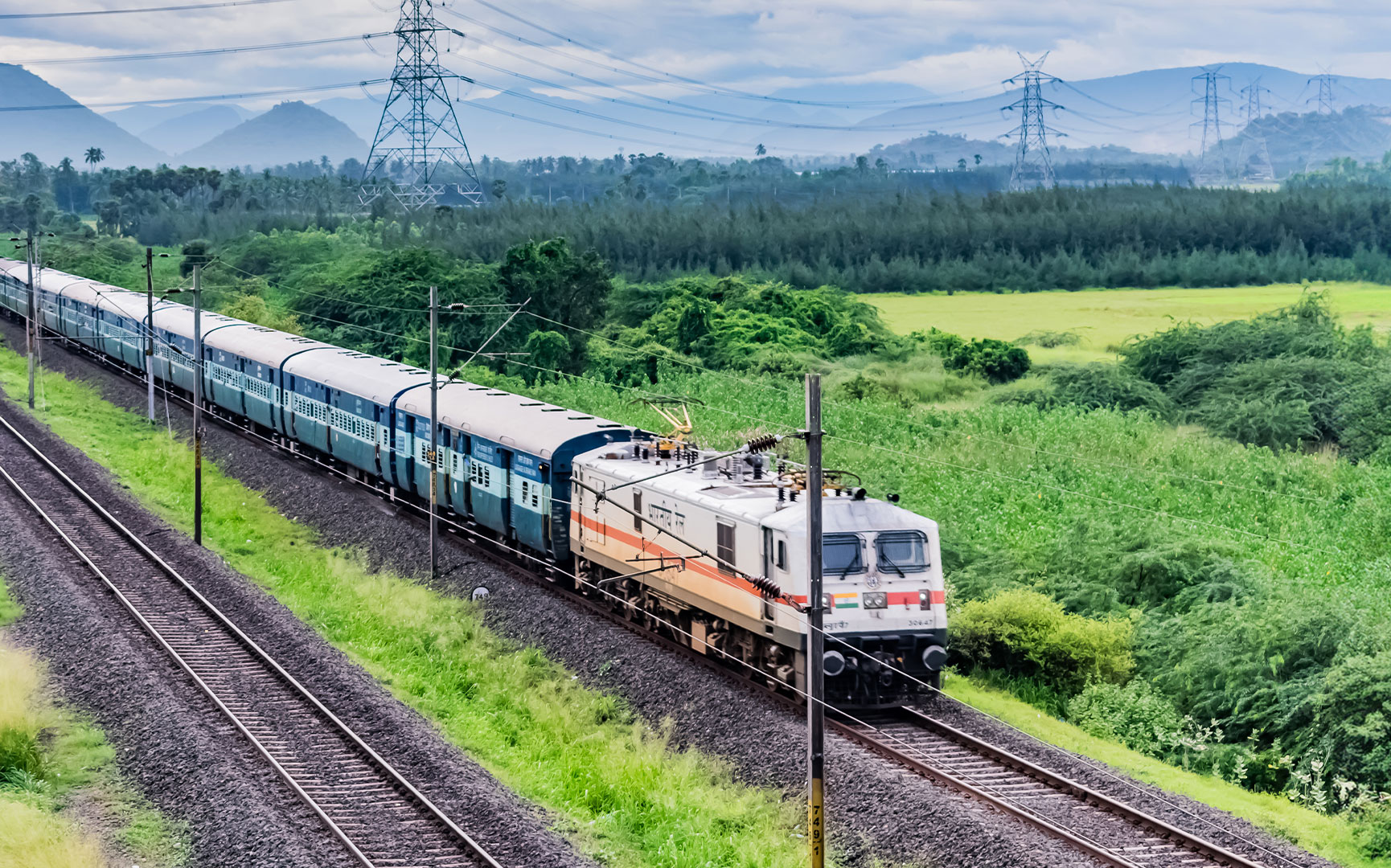